Table of Contents
** Minutes
How does integrated logistics work within the supply chain?
How an integrated supply chain meets customer demands
Integrated logistics for online stores: Pros and cons explained
Getting started with integrated logistics: What you need to know
Just like a company with an integrated marketing strategy can link different activities to understand how all efforts help attract and convert customers, an integrated logistics model can also streamline processes and information.
Understanding logistics is the most critical part in establishing an agile ecommerce supply chain, but this can’t be done in silos.
Proper logistics management helps you navigate and monitor inventory flow throughout the supply chain, from orders processed to last-mile delivery.
Ecommerce business owners are always looking for ways to optimise their ecommerce logistics to compete and better serve customers, and it’s not uncommon to implement what’s known as an “integrated logistics” model.
What exactly is integrated logistics?
Let’s take a closer look at what integrated logistics is, how it works, and how you can benefit from it.
What is integrated logistics?
Integrated logistics refers to a supply chain organisation method in which all parts of the supply chain, including departments, resources, and technology, are interconnected to operate together and improve efficiency.
How does integrated logistics work within the supply chain?
Integrated logistics works by establishing an efficient flow in operations, from product procurement to shipping. Here is an overview of the primary stages of the supply chain and how they work together within an integrated logistics model.
Procurement
In integrated logistics, procurement logistics is optimised with accurate planning and real-time inventory management.
This involves investing in technology and resources to enhance visibility into the procurement process to improve production forecasting. This can be done with inventory management software and/or partnering with an omnichannel fulfilment provider.
Raw materials and finished goods are procured based on forecasted demand and expected production lead times, so inventory is always available and supply chain operations aren’t disrupted in case of unexpected events, like a manufacturing closure or raw material shortage.
Understanding and calculating estimated lead times can help improve your inventory replenishment process and prevent stockouts.
Distribution
Once inventory is procured, it’s strategically distributed between different retail partners or distribution centres based on historical sales performance and consumer demand.
Distribution logistics is carried out efficiently, so that sales operations can continue smoothly without disruptions.
Again, visibility is key here, which includes having having access to real-time data.
Understanding the locations in which certain products are in high demand can help in deciding how much of each SKU to store in each location.
Fulfilment
With the right technology, once orders are placed, they are automatically processed and sent to the most optimal facility in which inventory is stored. This could be a rented warehouse or a fulfilment centre closest to the order’s destination.
From there, the fulfilment logistics process is automated, so orders can get out the door faster and get fulfiled efficiently.
Automated fulfilment involves picking and packing orders and getting them ready for fulfilment. Smart warehousing technology is used to speed up the fulfilment process while maintaining order accuracy.
For example, a warehouse management system can be connected to wearable devices or inventory scanners, so order pickers can instantly find where an item is stored and check the details to ensure the picked inventory matches the order.
Shipping
Shipping logistics can be streamlined with auto-generated shipping labels, and the best carrier is chosen based on the selected shipping option (subject to rates and destination). This allows orders to get shipped faster for faster deliveries.
Additionally, the business and the customer also get full visibility into order status with order tracking, as it travels to arrive at its final destination.
How an integrated supply chain meets customer demands
With many consumers expecting to receive their orders quickly, an integrated supply chain is crucial to meet these expectations.
When your processes, partners, vendors, and technology work together to provide visibility and accurate data, it enables you to meet customer demands more efficiently.
For example, inventory visibility will help you replenish stock on time so you don’t experience stockouts.
Real-time visibility is also crucial when dealing with multichannel logistics, because sales from multiple channels typically use the same pool of inventory, making the need for accurate stock level to be properly tracked and available so you don’t over-sell on any one channel.
Over time, you can use collective inventory and order data to improve demand forecasting, whether it’s deciding on the best locations to store inventory or stocking up for a possible surge in demand.
This might all seem costly and time-consuming, but there are many DTC logistics resources available for businesses of all sizes.
One of the most common options is partnering with a 3PL like ShipBob, which offers the technology, resources, and distribution network needed to build an integrated logistics model.
Instead of having to manage everything yourself (or lease one, let alone multiple warehouses), you can outsource fulfilment and leave it up to the experts.
“ShipBob has given us increased visibility thanks to the dashboard that allows us to easily manage stock and orders. That wasn’t possible for us before. Our relationship with ShipBob has been a game-changer for Quadrant, and it’s made my life so much easier.”
Will Kerr, Apparel Lead at Quadrant
Integrated logistics for online stores: Pros and cons explained
There are many ways to transform your current logistics operations into an integrated logistics model. To help you get started, here are some pros and cons.
Pro: Lower costs
When you have better visibility and coordination within the supply chain, it can significantly bring down the cost of logistics.
You’ll be able to identify inefficiencies and unnecessary steps that are increasing your logistics costs and look for ways to optimise them for better cost-efficiency.
Pro: Greater flexibility and efficiency
The increase in supply chain agility is a key benefit of integrating a logistics network. End-to-end supply chain visibility allows for increased collabouration between different teams, which further improves logistics efficiency.
This also provides you with the flexibility to quickly adapt in case of any unexpected disruptions, which is especially common with international logistics.
Con: ROI can take some time
While integrated logistics comes with a multitude of benefits for your business, it takes some time to show results. Not all processes and departments will integrate easily at the start, so you’ll need to wait a while for the impact to show.
It can be a large, upfront investment, which will take time to recuperate. But if you take the time to invest upfront, you’ll save a lot of headaches and challenges down the road.
Getting started with integrated logistics: What you need to know
The process of implementing integrated logistics requires strategic thinking and transparency across teams. Here’s what you need to know to get started.
Start with logistics planning
Integrated logistics will need lots of logistics planning with the goal to create a lean and cost-effective supply chain.
Logistics planning requires you to think through short- and long-term business goals and then to come up with a game plan on how you will achieve those goals to generate profit.
Look at all the different functions involved in your logistics model to identify how to improve communication and efficiencies through technology, partnerships, and resources. Taking this time to plan will help set you up to establish a resilient supply chain.
Streamline your logistics network
Operating a successful ecommerce business requires an integrated logistics network that can deliver quickly and cost-effectively.
The best place to start is to look at your existing logistics network and try to identify where you can streamline it for better collabouration.
- Is there a way to consolidate different stages in your network for better efficiency?
- Are there geographical areas where you need to expand your network through distributed inventory management for improved shipping speeds?
- Is there technology you can implement to collect real-time inventory data throughout your network?
To compete with larger brands and marketplaces, setting up your logistics network is key. Look into partners, technology, and other supply chain solutions to help you with this stage.
Consider outsourcing
In most cases, outsourcing logistics to the experts is often the best choice for better integration. As you expand your business to serve more customers and sell on new channels, it can be a challenge to manage inventory and fulfil orders from a single location.
To build a well-established integrated logistics network, many businesses will partner with a 3PL like ShipBob. All 3PLs are different, but ShipBob for example operates fulfilment centres in dozens of locations across the globe, which are all powered by the same fulfilment platform.
Partnering with a global fulfilment partner is the best way to expand domestically and internationally, because there’s no need to invest in your own network, which requires a lot of capital.
Even if you only ship domestically now, preparing for the future with a global solution will allow plenty of room for expansion.
“Utilising ShipBob’s network of fulfilment centres allows us to lessen our carbon footprint as well. We’re currently storing inventory in some of ShipBob’s US facilities, which means that when we receive an order destined for someplace like New York, we don’t have to ship it from all the way across the country.
By shortening the transit distance, we get to shorten transit time and reduce the amount of pollution produced in the shipping process. Even in the final stages of fulfilment and last-mile delivery, ShipBob enables us to stay true to our mission!”
Juliana Brasil, Director of Operations at Food Huggers
ShipBob’s integrated solution in 4 steps
ShipBob’s global omnichannel fulfilment solution provides the expertise, technology, and resources needed to establish an integrated logistics network. Here is an overview of how ShipBob operates.
Step 1: Procurement planning
Understanding and calculating estimated procurement lead times can help improve your inventory replenishment process. ShipBob’s expertise and technology provides you with the right data and resources to help you better plan for ordering more inventory.
With ShipBob, you can set automatic reorder point notifications to order and ship inventory in time.
ShipBob also offers an easy-to-follow warehouse receiving process, allowing merchants to create and fill out a Warehouse Receiving Order (WRO) digitally and have manufacturers add a label to each shipment with the barcode visible.
From there, ShipBob uses its proprietary warehouse management system (WMS) to pull up data on the order and make sure the the inventory is accurate and stored in the right place.
We don’t always know exactly when our inventory shipments will arrive from our suppliers, and other 3PLs told us they would reject our shipments if they didn’t arrive on a certain time and date. ShipBob is a lot more flexible because of their technology, and our representative helped explain how receiving works, which was a big plus.”
Adelina Zotta & Connor Westby, Co-Founders of NutriPaw
Step 2: Inventory storage and management
ShipBob can store your inventory in one or many strategically located fulfilment centres (of your choice), so that your business can ship quickly and cost-effectively anywhere.
You can store inventory across locations and still manage everything in one place with ShipBob’s powerful, centralised fulfilment platform that integrates with your existing logistics systems.
ShipBob’s technology accurately keeps track of current and historical inventory levels to help you make better decisions on when to replenish inventory and even where to store it.
From ShipBob’s dashboard you can:
- Get full visibility into real-time inventory levels.
- Review storage and other integrated logistics costs.
- Set automatic reorder notification points.
- Track historical sales data and other metrics for use in demand forecasting, including tools to view how quickly increases in demand will deplete inventory.
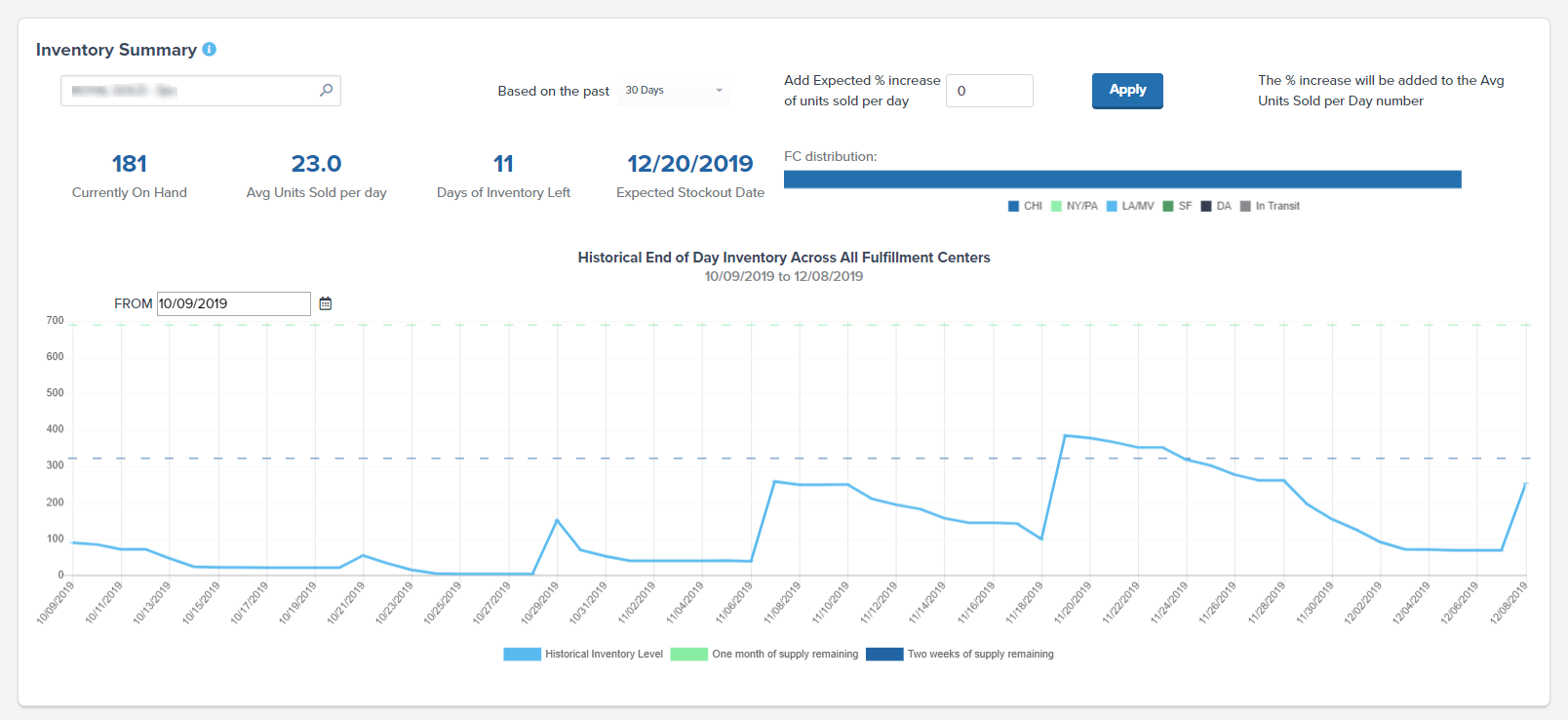
Step 3: Order placement and processing
ShipBob allows you to simplify retail logistics with software that integrates with your online store(s) and other sales channels.
This allows you to automate your order receiving and processing systems by automatically moving orders to fulfilment once they’re placed online.
Once an order comes in, it is routed to the nearest fulfilment centre location to speed up delivery times and reduce shipping costs by shipping from closer to the end customer.
Step 4: Fulfilment and shipping
After orders are automatically processed and sent to the optimal ShipBob fulfilment location, the picking and packing process begins.
Shipping labels are generated using the ideal, most cost-effective carrier for each order. ShipBob partners with regional, domestic, and international shipping couriers ,negotiating rates on your behalf.
Logistics is something you never think about until it stops working, and we’ve never come to that point with ShipBob. Everything just works. We are super happy with ShipBob and very impressed by how well they’ve pumped out our large volume of orders.”
Sergio Tache, CEO of Dossier
To learn how ShipBob can help you build an integrated logistics network, fill out the form below to request custom pricing.
FAQs
Integrated logistics FAQs
Below are answers to the top questions about integrated logistics.
What is meant by integrated logistics?
Integrated logistics refers to a supply chain organisation method that involves connecting different departments and processes within the supply chain for better efficiency.
What are the characteristics of integrated logistics?
Visibility, automation, coordination, and communication are some of the key characteristics of integrated logistics. Streamlining information across all logistics processes enables a more seamless, interconnected operation.
What is the difference between traditional logistics and integrated logistics?
Integrated logistics consists of similar functions as traditional logistics, except that all the processes, departments, and systems are closely synced, often using a centralised technology stack. This enables a more seamless passing of information so no parts of the supply chain are siloed.