Warehouse Control System Guide
The ecommerce supply chain relies on good warehouse management, so orders are quickly and accurately fulfilled.
To achieve this, inventory needs to consistently move through multiple warehousing processes until it’s finally ready to be shipped out to the customer.
To better oversee the flow of inventory and its associated activities, some businesses may use a warehouse control system (WCS) that works seamlessly with their existing warehouse management system (WMS).
Implementing a WCS might seem like a time-consuming and costly endeavor, but it’s not as complicated as you might think.
So, what do you want to learn?
Request WMS Pricing
Let’s talk. See if ShipBob’s warehouse management system is right for your warehouse.
A fulfillment expert will get back to you shortly. Privacy Policy
Distributed Inventory: How Multiple Fulfillment Centers Can Reduce Transit Times & Shipping Costs
Ship faster & save money by splitting your inventory. Learn how.
Download the guide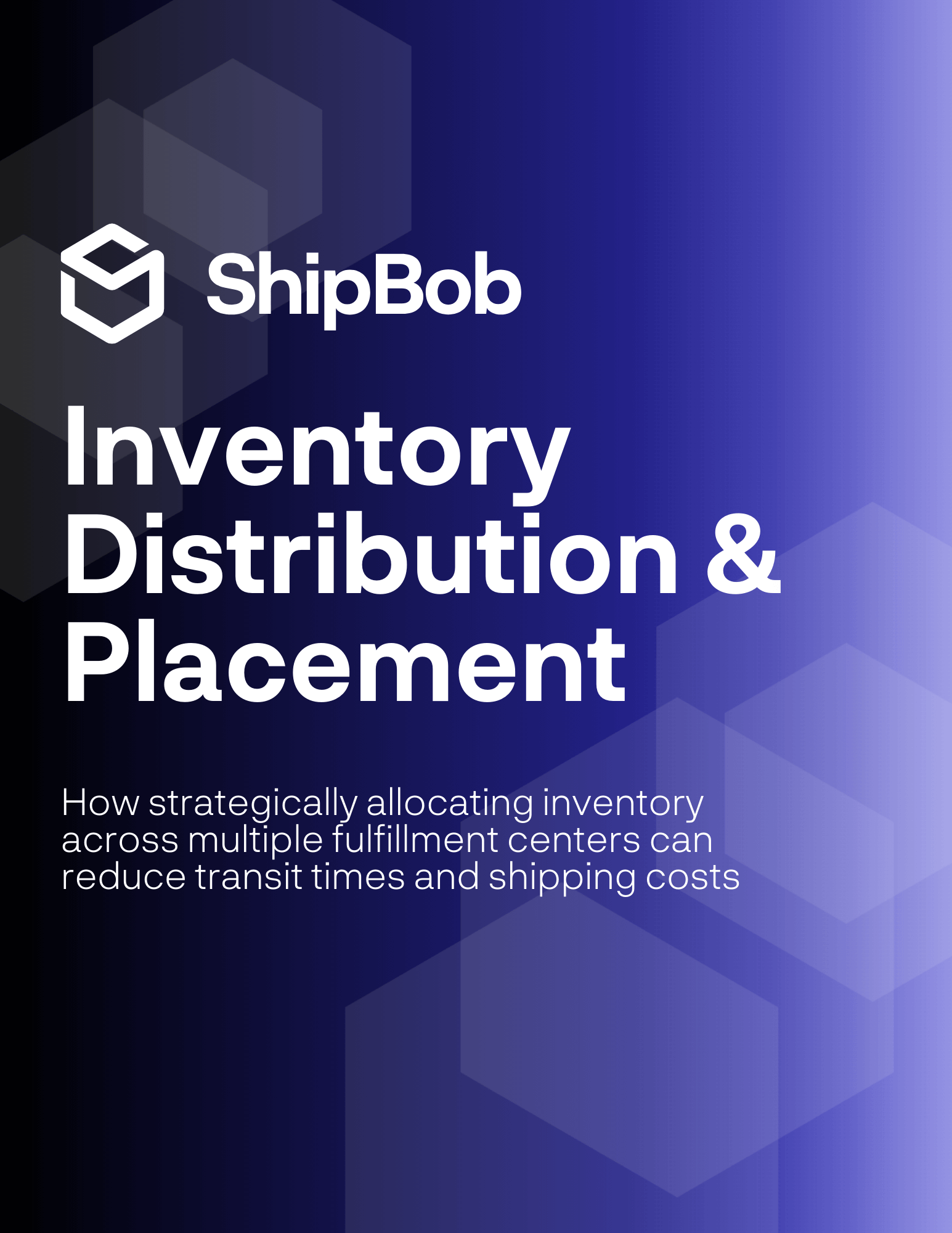
What is a warehouse control system (WCS)?
A warehouse control system is a software solution used for directing the flow of inventory within a warehouse or distribution center.
It helps to coordinate tasks between different subsystems, such as carousels, sorters, conveyors, and palletizers, so the flow of inventory runs smoothly, from stowing inventory to shipping.
Essentially, a WCS helps to optimize your warehousing operations and control inventory until your products are ready to be shipped.
ShipBob’s Warehouse Management System (WMS)
ShipBob’s WMS helps your warehouse reduce picking errors, manage inventory in real time, and fulfill orders faster.
Benefits of a warehouse control system
A WCS is a type of smart warehousing solution that helps ecommerce businesses keep their warehouse organized, while saving time and costs and increasing visibility into day-to-day tasks across warehouse employees.
More specifically, a WCS does this by helping a business manage its equipment, improve its storage strategy, and retrieve products efficiently.
Equipment control
A WCS is particularly useful for businesses that use high-tech equipment and machines (which is often the case for businesses with complex picking and loading requirements).
By coordinating different tools so that they work together seamlessly, a WCS ensures warehousing workflows and functions run smoothly from receiving, to fulfillment, to shipping.
Storage optimization
Using a warehouse control system, a business can strategically allocate storage space and manage warehouse capacity for efficiency and cost savings.
A good WCS will make sure that new inventory is assigned to and reaches the correct temporary and permanent storage location, helping a business save time, minimize inventory shrinkage, and keep storage costs low.
Product retrieval
Ecommerce businesses with highly automated warehouses can also use a WCS to improve product and picking routes. A WCS can help optimize picking flows to shorten picking time, and make it easier to find and pick products in fulfillment.
How does a WCS work?
A warehouse control system works by performing and supporting the following key functions:
- Exchanges essential information with a higher-level software application such as a WMS, so material handling functions are automatically performed and the flow of products within the warehouse is tracked.
- Communicates in real-time with material handling equipment and subsystems, allowing them to coordinate all the activities and subsequent movements of automated equipment.
- Assigns cartons to divert them to the right locations.
- Determines the most efficient route for products and then controls the direction of material handling equipment such as conveyors, sorters, carousels, and scales to ensure products are transported accordingly.
- Uses data from system-level sensors and controllers to provide real-time monitoring and management of automated warehousing systems. This helps to improve efficiency and enables quick diagnostics in case something goes wrong or isn’t working.
What are the 4 pillars of a good WCS?
Whether you’re trying to implement a new WCS or optimize an existing one, it’s important to understand what makes a good WCS. Here are the four pillars a WCS should have, so you know what to look for and how to optimize your existing system.
1. A flexible interface
A good WCS should offer a flexible and user-friendly interface that you can seamlessly implement across multiple devices with minimal risks.
This includes having the ability to integrate with existing systems to minimize the risk of disruptions and disconnects between different warehousing activities.
A smooth integration will help to streamline and simplify your warehouse operations as it enables you to manage your inventory, warehouse labor, and equipment all in one place.
2. Planning tools
A warehouse control system with good planning tools can make your operations much more efficient.
For example, you can use a material flow planning tool to visualize your material flow and simulate it, so all the material handling equipment is efficiently utilized and all the integrated subsystems are working together smoothly.
You can then use this to plan for an optimal material flow that enhances efficiency.
Additionally, a good WCS allows you to control the material flow based on different product characteristics. That way, you can intelligently group orders to make the retail fulfillment process for retailers like Walmart and Target as smooth as possible.
3. Automation control system
Since the goal of using a WCS is to save time and optimize your warehouse processes, automation should be central to the system.
A good WCS should automate tasks and easily integrate with your existing warehouse infrastructure, including equipment like conveyor control systems, sortation control systems, and automated storage and retrieval systems (ASRS).
4. System visibility
One of the most critical components of a WCS is system visibility. You should have access to real-time monitoring and tracking so you can get transparency into the daily activities across your warehouse.
This will give you better control over your operations while ensuring enhanced compliance with industry standards and improved workload balance.
You should also be able to set up exception alerts to immediately identify any issues and fix them before they turn into bigger ones.
How does a WCS differ from WMS and WES?
During the process of setting up a robust warehousing operation, you may come across different SaaS WMS offerings designed to help you with warehouse management.
In addition to a warehouse control system, you may be looking at solutions such as a warehouse management system or a warehouse execution system (WES). Each solution serves a specific purpose and has a unique core function to improve your warehousing operations.
So how does a WCS differ from these two? Let’s first take a look at the definition of each type of system to gain a better understanding of their differences.
What is a WMS?
A warehouse management system (WMS) is a warehouse technology that enhances inventory visibility and tracks activity within a warehouse.
A WMS functions across different warehousing processes, from warehouse receiving and inventory management, to fulfillment and shipping.
WMS platforms help businesses optimize their storage space, track and locate inventory quickly, stay on top of inventory replenishment, and even eliminate the need for manual inventory counts to avoid common inventory issues, such as stockouts, dead stock accumulation, and inventory discrepancies.
A WMS can integrate with enterprise resource planning (ERP) software. If you outsource fulfillment, many third-party logistics companies offer a WMS as part of their fulfillment service, using it in the fulfillment centers where your products are stored and fulfilled. This allows businesses that outsource to track warehouse activity without being involved in the day to day (or running a warehouse themselves).
Every WMS is different, but a basic WMS should come with the following capabilities:
- An input system to receive and stow inventory in various locations
- Real-time inventory tracking
- Warehouse picking list generation
- Automatic order tracking
What is a WES?
A warehouse execution system (WES) is a hybrid platform that combines some of the features of traditional WMS with the capabilities of a WCS.
A WES provides real-time inputs for coordinating work and equipment functions in a highly automated facility. WES platforms direct and manage the physical flow of goods throughout different warehousing functions — from warehouse receiving to shipping.
WES platforms typically focus more on goods-to-person technologies. They also involve semi-automated processes, where warehouse staff is involved.
A warehouse execution system generally comes with features such as automated picking management, replenishment management, and packing station management.
What are the major differences between these systems?
Although the capabilities of these three systems sometimes overlap, there are a few key differences you should keep in mind, and they typically fall in this order of utilization as a business and warehouse grow in size.
A WMS is primarily responsible for managing your overall operations and the flow of inventory within the warehouse. It specializes in assigning and delegating tasks to warehouse workers and tracking orders from the moment they’re received until they’re shipped out.
Meanwhile, a WCS is specifically responsible for controlling the physical flow of inventory using material handling equipment and systems. It typically integrates with the WMS and becomes a part of it, while offering an additional layer of control over the movement of product.
On the other hand, a WES can be considered as a next-gen WCS since it essentially performs similar tasks but possesses some of the features of a WMS. It adds to the WCS by providing a higher level of warehouse management.
Overall, a WES doesn’t have enough management features to entirely replace a WMS. Instead, it’s designed to work in alignment with your warehouse management system to perform the functions that your WMS doesn’t cover or can’t do well on its own.
WES, WCS, WMS: which one(s) is right for you?
Typically, the larger your business’s warehousing operations, the more layers of control you’ll want to build into your warehouse management.
For example, a very large enterprise warehouse that moves hundreds of SKUs, relies heavily on automation, and houses many supply chain operations would benefit from using a WES, WCS, and WMS.
On the other hand, a smaller business with lighter order volume and fewer SKUs may find that a WMS alone gives them the visibility and organization they need. In this case, there’s no need for a WCS or WES.
But size is not the only factor to consider. Each system caters to different needs, and the best-suited solution for your business will depend on what you are looking for:
- If your business needs a means to control, organize, and automate how inventory is physically moved throughout the warehouse, consider a WCS.
- If your business needs overarching visibility and control, or in-depth analytics on multiple supply chain operations, consider a WMS.
- If your business needs a hybrid solution that manages inventory movement while providing some analytic capabilities, consider a WES.
How ShipBob can help you take warehouse management to the next level
ShipBob is a global leader in warehouse management, offering a best-in-class WMS for in-house fulfillment as well as fulfillment services, including an omnichannel fulfillment network and an advanced cloud-based fulfillment platform.
ShipBob’s fulfillment centers operate using a proprietary WMS, which gives ShipBob merchants full visibility into the fulfillment process and warehousing operations.
“With ShipBob, there are so many checks and balances, so we don’t screw up picking. It’s been great. We can track our inventory in real time now, knowing the number of units we have for each product and where they all are in our warehouse.”
Rick Corbridge, COO at Infuze Hydration
ShipBob’s fulfillment platform, which integrates with its WMS that can also be used as a standalone platform in a brand’s own warehouse, connects with multiple ecommerce platforms and sales channels, allowing you to start off small and expand into new markets with ease as your business grows.
Once you connect your store(s) to ShipBob’s platform, as soon as orders are placed, they’re sent to the closest ShipBob fulfillment center location to begin the process of picking, packing, and shipping.
By partnering with ShipBob, you save time and costs while improving fulfillment processes, so you can scale your operations and fulfill more orders.
“Prior to ShipBob, we’d ship 300 orders/day. On that first night, we shipped 700 orders in the same timeframe. That speed is so valuable and so seamless.”
Rick Corbridge, COO at Infuze Hydration
For in-house fulfillment, ShipBob’s WMS is a full-stack fulfillment and warehouse management solution designed for up-and-coming brands with their own warehouses. This solution eliminates the need to stitch multiple systems and platforms together and instead, lets you manage everything in one place.
To learn more about ShipBob’s omnichannel fulfillment solutions, contact our team today.
Warehouse control system FAQs
Here are answers to the top questions about warehouse control systems.
How does a warehouse control system work?
A warehouse control system works by integrating with a WMS to oversee all activity within a warehouse. It controls material handling equipment across different subsystems to ensure that they’re working together.
What systems are used in a warehouse?
Warehouse management systems (WMS), warehouse control systems (WCS), and warehouse execution systems (WES) are common systems used in a large scale warehouse. The most common system used is a WMS, which both WCS and WES systems can integrate with as a business grows and has more complex warehousing needs and automation used.
What is the main objective of a warehouse control system?
The main objective of a warehouse control system is to ensure that the physical flow of goods is running smoothly by monitoring warehouse automation, including equipment and machines used to move inventory throughout different stages.