Warehouse Receiving Guide
How a business receives inventory at a warehouse will impact other areas of the retail supply chain, including inventory management, picking, packing, and shipping.
As your business grows, the warehouse receiving process can get messy pretty easily. And a poor warehouse receiving process can lead to stock control issues and higher operational costs.
In this article, you will learn more about the warehouse receiving process, the benefits of optimised warehouse receiving, and how ShipBob can take care of fulfilment and inventory receiving for you using our standardized processes, fulfilment network, and expertise.
So, what do you want to learn?
Request WMS Pricing
Let’s talk. See if ShipBob’s warehouse management system is right for your warehouse.
A fulfilment expert will get back to you shortly. Privacy Policy
What is warehouse receiving?
Warehouse receiving is the first step of the ecommerce fulfilment process and refers to the process of delivering, unloading, and storing ecommerce inventory in a warehouse or fulfilment centre. A well-established warehouse receiving process can help make inventory management and fulfilment easier, cost-effective, and more efficient.
ShipBob’s Warehouse Management System (WMS)
ShipBob’s WMS helps your warehouse reduce picking errors, manage inventory in real time, and fulfil orders faster.
The standard warehouse receiving process
Warehouse receiving is not simply a matter of purchasing inventory and having it delivered to your warehouse; rather, it involves several key steps that must be done right to ensure the right items and quantity are being delivered and stored correctly. Here is an overview of the standard process of receiving goods:
1. Create proper documentation and then send your inventory
Before inventory is ordered and delivered, a business owner must complete pre-receiving tasks before sending inventory to a warehouse.
During this stage, the business owner decides how much of each item will be shipped in how many containers, as well as determine packaging requirements for each item (e.g., labelling criteria, the number of packages loaded per pallet, and acceptable package sizes and weights).
If you partner with a third-party company (3PL), you will want to check their pre-receiving requirements as most of them have their own process for how to send inventory to their warehouse(s) and often steps you must complete before you send them your inventory.
In most cases, you will need to fill out a Warehouse Receiving Order (WRO) label and attach it to each shipment with the barcode visible. This makes it easy to scan the shipment using a warehouse management system (WMS) to pull up data on the order and make sure the receiving inventory is accurate and stored in the right place.
2. Receive and unload stock
If you manage a warehouse, the next step is to have warehouse receiving staff meet the shipper at a loading dock and unload the necessary cargo. Receiving staff should be standing by to discuss questions or concerns regarding the shipment with the delivery driver.
Ideally, truck beds should be packed back-to-front in the reverse order of the delivery schedule so that warehouse workers can unload their inventory immediately without having to move another other cargo in the way.
Depending on the size and volume of the cargo, unloading sometimes requires heavy lifting equipment such as forklifts and pallet jacks.
3. Count and confirm inventory
As the cargo is being unloaded, the warehouse staff checks the contents of each delivery, including the quantity, the integrity of seals, the product codes/SKUs, and the overall condition of the cargo to ensure that what’s in the boxes matches what is listed on the WRO and is expected to arrive.
Stock counting, inspection, and general warehouse operations can be time-consuming. To avoid hours at the loading dock, some merchants require warehouse staff to count boxes or pallets, rather than individual items, or choose to perform periodic random inspections. Or, you can use an inventory scanner system to automate this process, or leave it up to a 3PL to take care of.
4. Store and file product
Once all inventory is unloaded and inspected, the final step in the warehouse receiving process is organising and storing new inventory in the warehouse.
This step looks different for each business, depending on the type of warehouse, the quantity and size of their items, and whether a business relies on a 3PL partner for inventory storage.
Depending on the size and quantity of products, inventory can be stored either on a palette, a shelf, or a bin. If you partner with a 3PL, it’s up to their fulfilment staff to store your inventory in the most efficient and cost-effective way to save you on carrying costs.
If you own or lease a warehouse, businesses are in charge of handling storage based on their fulfilment process. Your logistics staff will need to take charge of completing all documentation and verification, as well as inputting the receive inventory’s information into the WMS or manually track it.
Where most businesses get receiving wrong
The goal of warehouse receiving is to unload, check, and store inventory efficiently and accurately, and to make sure all inventory is accounted for.
When warehouses or businesses don’t have a set of procedures or a checklist for unloading and receiving, they risk ending up with inaccurate or lost inventory, which can impact accurate inventory counts.
To avoid dealing with inaccurate inventory tracking, business owners should provide their warehouse staff with resources that clearly communicate a streamlined, step-by-step task list to follow when receiving, as well as ordered lists of questions to ask and details to check.
For example, ShipBob uses a step-by-step WRO process to check inventory being received and to ensure it gets stored correctly. We require every customer to fill out a WRO from the ShipBob dashboard for each box and/or pallet of inventory they order and book or reserve a dock appointment, which helps us understand how much of each item is being shipped and to which fulfilment centre location and plan for capacity.
If a box or pallet does not contain exactly what is listed on the WRO, we will put a hold on your items and move the boxes/pallets to an on-hold receiving status. This creates an Unidentified Receiving Order (URO). We will notify you about the URO via email and ask that you create a new WRO for the order or resolve the discrepancy. This ensures minimal delay in processing your inventory and getting it on the shelves.
What happens when you optimise your warehouse receiving?
Optimising your warehouse receiving process is an investment that will set your fulfilment logistics strategy up for success. Since it’s the first step in the fulfilment process, a structured warehouse receiving process will help you properly manage inventory and make sure the right items and quantity of those items are available to be fulfilled.
Here are just a few of the benefits you can expect when you optimise the warehouse receiving process.
1. More accurate stock counts
Accurate stock counts are essential to a brand’s ability to manage their inventory, avoid stockouts, forecast demand, reduce inventory shrinkage rate, and maintain a healthy profit margin.
By taking the time to develop a comprehensive checklist for your staff to follow will help with inventory control—especially if you use automated technology to make the process easier, such as using a new inventory scanner, so stock levels can be updated in real-time. This also to ensures that the contents of a delivery matches the original order.
2. Fewer stockouts and dead stock
Stockouts (not having enough items in stock to fulfil order) can cause customers to look elsewhere and can also lead to negative reviews that can impact your online brand’s reputation.
On the other hand, overstocking (known as dead stock) leaves business owners with an inventory surplus that will not deliver a return on investment, let alone a profit.
An optimised warehouse receiving process will help prevent both issues, and issues with inventory receiving can be caught early on—such as the supplier not delivering the quantity ordered.
3. Efficient inventory storage
Optimising your warehouse receiving process can also strengthen your inventory storage system by making sure inventory is being stored in the most efficient, cost-effective way possible.
Using a WMS, once the inventory is scanned when received, staff can retrieve instructions on how to unpack and store the inventory, as well as how to pick, pack, and ship items once sold.
How to optimise your warehouse receiving
There are several ways to optimise the warehouse receiving procedure. To help you get started, here are some best practices that you can implement–whether you manage your own warehouse or partner with a 3PL like ShipBob.
Deploy inventory management systems
Inventory management systems help ecommerce businesses optimise their entire supply chain (not just the process of receiving goods) by automating the process.
They give you insights into real-time inventory counts and more accurate numbers for inventory accounting purposes.
Once your existing inventory is loaded into an inventory management system, you’ll be able to view real-time stock levels and see your inventory numbers change immediately after the warehouse receiving process.
This type of software also makes it easy to set automatic reorder points to remind you it’s time to order more products based on inventory forecasting predictions for each SKU.
Track your inventory metrics
A proper warehouse receiving process will make tracking inventory and logistics costs much easier—especially if you store inventory in multiple warehouses or fulfilment centres. By using technology to manage all inventory, you’re able to monitor important distribution metrics all from one central dashboard.
For instance, with ShipBob’s built-in analytics reporting tool, you can keep track of:
- Average storage cost per unit
- Total number of bins/shelves/pallets currently in use
- How much inventory is stored at each location
- And more
By monitoring these metrics and translating them into meaningful change, business owners can transform their data into a competitive advantage.
“Storing inventory in different regions is key to reducing costs and transit times. From expanding into a second ShipBob fulfilment centre, we are able to offer 65% of our customers with 2-day shipping, up from 32% by only having a single West Coast facility. Soon, this will be 100%.
Not only is this better for our customers, but we also gain a 13% savings to our bottom line.”
Pablo Gabatto, Business Operations Manager at Ample Foods
Run inspections
A few minutes of caution upfront prevents the hassle and expense of sending back damaged, missing, or incorrect inventory after it’s too late. Periodic inventory audits such as physical counts and cutoff analyses also catch inventory imbalances before they get out of hand, and will inform your next round of warehouse receiving.
ShipBob’s built-in inventory management tool can help you conduct inventory audits as needed, and gives you real-time updates on stock levels, damaged products, and specific SKUs to make tracking inventory quicker and easier.
Double-check documents
No one likes paperwork, but you will save the trouble of correcting mistakes by double-checking that receiving inventory matches your purchasing order.
Implementing a system for all receiving and shipping documents, in which each type of document has a numbering system and different forms are labelled in sequential order, also makes it easier for staff to check paperwork thoroughly and identify missing inventory.
For instance, ShipBob’s WRO system is designed to make sure you have the information you need to send us your inventory, so everything is accounted for and stowed away properly.
From the dashboard, you easily create a WRO with information on where you’re sending inventory to, the quantity of each SKU being sent, how it will be shipped to us (e.g., parcel, palletized container, or floor-loaded container), and create a box label for each shipment.
With this information, we’re able to make sure what is sent to our fulfilment centres is accurate, so we can store and update inventory levels accordingly.
“ShipBob’s customer service has been great. I have no trouble placing orders and submitting warehouse receiving orders.”
Lee Nania, Founder of SubSubmarine
Improve warehouse receiving with a WMS
To optimise your warehouse receiving process, you need the right tech in place. ShipBob has a best-in-class warehouse management system (WMS) for brands that have their own warehouse and need help managing inventory in realtime, reducing picking, packing, and shipping errors, and scaling with ease.
With ShipBob’s WMS, brands with their own warehouse can even leverage ShipBob’s fulfilment services in any of ShipBob’s fulfilment centres across the US, Canada, Europe, and Australia to improve cross-border shipping, reduce costs, and speed up deliveries.
How ShipBob optimises warehouse receiving for faster shipments
ShipBob is a 3PL that helps business owners optimise their supply chain. ShipBob takes the fulfilment process seriously, and it starts with a proper warehouse receiving procedure.
ShipBob implements a number of best practices when receiving customers’ inventory. First and foremost, ShipBob’s standardized WRO process is designed to cut unnecessary time and complication out of the warehouse receiving process by having your inventory sent directly to one of our orderfulfilment centres.
Once it arrives, your inventory is unloaded, checked, and unpacked by expert warehousing and fulfilment workers trained to store inventory in the most spatially-efficient manner possible; all while being tracked in our inventory management software. From the ShipBob dashboard, you can track the status of all WROs and check if WRO was received on time based on our service level agreements (SLA).
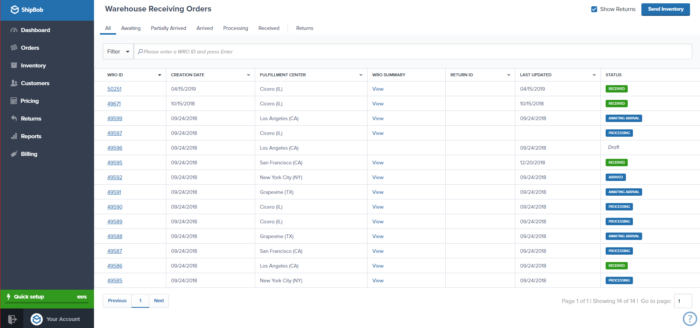
ShipBob stores each SKU in a separate, dedicated storage location within our fulfilment centres (either on a shelf, in a bin, or on a pallet, even equipped for lot tracking) and enters new inventory using our WMS technology that tracks real-time inventory as your stock depletes.
Once inventory is stowed, ShipBob merchants can track inventory in real-time, set reorder points, forecast inventory needs, and more, all from one dashboard.
With ShipBob, ecommerce business owners can spend less time and money on inbound and outbound logistics, knowing that warehousing and fulfilment are being taken care of. To learn more about ShipBob’s capabilities and to request pricing, click the button below.
Optimise your warehouse’s capacity with ShipBob’s WMS
To optimise warehouse capacity, you need the right tech in place. ShipBob’s WMS is best-in-class software for brands that have their own warehouse and need help managing inventory in real time, reducing picking, packing, and shipping errors, and scaling with ease.
Warehouse receiving FAQs
Here are answers to some of the most frequently asked questions about warehouse receiving.
How do I improve warehouse receiving?
There are several ways to improve warehouse receiving. Tools like inventory management or warehouse management software go a long way in improving warehouse receiving, as they allow you to quickly scan new inventory and make sure it’s accurate and is stored correctly. Always measure deliveries against order documentation to reduce inventory issues in the long run.
What is involved in warehouse receiving?
The standard warehouse receiving process comprises several stages. First, you must establish receiving requirements and order inventory through the proper channels. When the inventory shipment arrives, warehouse staff unload the cargo, count the stock delivered, and inspect it to make sure it exactly matches what was requested before storing each item in its designated location in the warehouse and updating inventory levels.
What is putaway in warehousing?
Putaway refers to every stage involved in the process of receiving goods.
It typically refers to the initial placement of a purchase order with a supplier or vendor, all the way through to the landing of orders in your receiving dock and subsequent packing into their respective warehouse locations. Quantity and quality checks are also part of the putaway process.
What is pre-receiving in a warehouse?
Pre-receiving is a preparatory stage of the warehouse receiving process that ecommerce business owners must complete before any inventory is shipped or delivered to a warehouse. In this stage, you must decide on receiving requirements and fill out appropriate documentation, labelling materials, and order forms needed to ensure new inventory is received by the warehouse properly.