Warehouse Inventory Management Guide
Managing a warehouse and your inventory is an ongoing cycle that never ends as long as you are running a business.
In this article, learn why warehouse inventory management is important, industry best practices you can implement, and how a third-party logistics (3PL) can help.
So, what do you want to learn?
Request WMS Pricing
Let’s talk. See if ShipBob’s warehouse management system is right for your warehouse.
A fulfilment expert will get back to you shortly. Privacy Policy
What is warehouse inventory management?
Warehouse inventory management is a process that involves receiving, storing, and tracking inventory in a warehouse; managing warehouse staff; and optimising storage space and costs; all of which directly impacts fulfilment, shipping, and the customer experience.
Why is warehouse inventory management important to your business?
How you manage inventory in any warehouse influences how much you spend on logistics costs and how efficient your supply chain runs.
When you think of warehouse inventory management, it’s likely that storing inventory on warehouse racks comes to mind.
However, there is so much more to warehouse inventory management than you might expect, and this is a leading reason why many companies outsource this function of their business to a third-party like ShipBob.
Here are five reasons why direct-to-consumer (DTC) brands that manage their own warehouse should invest in improving warehouse inventory management:
1. Improves order fulfilment accuracy
If your warehouse is not well-planned and managed, it will cause delays and issues during the order fulfilment process. Most issues with orders stem from disorganized inventory, poor picking and packing processes, and a lack of stock control in your warehouse.
By implementing better warehouse management processes and technology, you can greatly improve order accuracyand fulfil orders more quickly.
2. Boosts warehouse productivity
When warehouse inventory is stored and recorded properly and manual daily tasks are automated, it gives your staff the time and mental bandwidth to focus on more strategic tasks, such as logistics expansion and growth.
Thinking through ways you can help your staff become more efficient will not only save on labour costs, but it will also help you get orders out the door faster and more accurately.
3. Faster shipping and deliveries
How you manage your inventory in a warehouse can also impact shipping speed. There are severals way to optimise warehousing processes to speed up last-mile delivery, from automating order processing to expanding your distribution network by splitting inventory across multiple fulfilment centres.
Many DTC brands choose to automate shipping by implementing tools that can help speed up the shipping process, such as automatically updating stock levels and pushing ecommerce order tracking to customers.
Finding ways to automate the shipping process enables you to increase output, so you can easily manage a larger volume of orders.
4. Saves you money
Proper warehouse inventory management can save you money, including labour, storage, and fulfilment costs.
Optimising storage, investing in warehouse automation, organising inventory to speed up the picking and packing process, and implementing technology to automate tasks and reduce human error are just a few of the ways you can improve your bottom line by optimising your supply chain.
However, it’s worth noting that renting a warehouse comes with a cost. In fact, most logistics warehouse tenants are expecting a 10% rate hike starting in 2021. That’s why more and more online brands are choosing to outsource warehousing to save on not only time but money, so they improve supply chain and profit margins.
5. Increases customer satisfaction
A warehouse that performs well is one that delivers customer orders accurately and on time. By making warehouse inventory management a priority, you ultimately improve customer satisfaction through faster shipping times, reduced shipping costs, and higher order accuracy rate.
Additionally, if there is an issue with an order or a customer has to make a return or exchange, proper warehouse processes and inventory management can also improve the returns management process, so you can quickly process returns and restock items.
5 warehouse inventory management processes
When done right, warehouse inventory management can help keep your retail supply chain moving, from receiving inventory efficiently to fulfilling and shipping orders out quickly. Here are five warehouse inventory management processes that are worth implementing:
1. Warehouse layout optimisation
Optimising your warehouse space is the first thing to consider when managing a warehouse. How will you organise inventory to make the picking and packing process more efficient while saving on inventory carrying costs?
To optimise your warehouse layout, the first step is to assess the current warehouse layout and determine if it suits your order fulfilment process.
One common warehouse optimisation practice is warehouse slotting, which helps to simplify the picking and packaging stages by storing inventory based on what makes the sense of the picker (such as storing frequently ordered products by one another, or making the best use of space by product type, size, weight, and location). Not only does this process optimise space but it also improves productivity.
Taking the time to optimise your warehouse means you can delay expanding and spending more money on space than you actually need.
2. Warehouse inventory control tracking and recording
Managing inventory is one of the most important parts of running an ecommerce business. The best way to better control stock is to invest in inventory management software and other tools designed to:
- Automate the order picking process.
- Track inventory in real-time.
- Forecast inventory demand.
- Generate inventory reports.
- Optimise inventory levels.
- And much more.
To track inventory, you need both reliable inventory storage system and inventory software to assist with these types of tasks.
If you’re doing the self-storage route or renting a warehouse, you can find software or inventory apps that manage and track your inventory easily, as well as reduce the time needed to conduct ongoing inventory audits and warehouse audits.
Larger, more established brands usually invest in an ERP inventory system with all the bells and whistles. However, many 3PLs offer the necessary inventory management tools as part of their warehousing and fulfilment service, like ShipBob.
3. Picking and packing
The picking and packing process should be optimised as much as possible to help support your picking and packing team and reduce human error. For instance, you could create a “golden zone” for your fastest-moving high-demand products (i.e., the most accessible location of the warehouse).
Another common warehouse practice is known as batch picking, a process that consists of collecting inventory for identical orders at once, rather than picking items one order at a time or picking orders with different SKUs, so the picker is able to reduce the number of trips to the same location(s).
4. Shipping
If you self-fufill orders, then you know it can be time-consuming process, not to mention there are several hidden costs associated with self fulfilment.
Some online brands choose the dropshipping or blindshipping methods instead, which consists of having the manufacturer take care of shipping. Dropshipping also eliminates the need for the merchant to manage a warehouse or inventory.
However, there are a lot of downsides to dropshipping, including a lack of quality control, visibility into logistics operations, and the inability to enhance the customer experience.
That’s why most ecommerce businesses turn to a reliable 3PL partner like ShipBob to take care of fulfilment and shipping for them. Many 3PLs also offer distributed inventory due to their expansive fulfilment network, negotiated shipping rates from major couriers, and the ability to track orders all from one dashboard.
5. Reporting and optimising
Investing in a warehouse management system (WMS) can help you determine operational performance and offer inventory reports across the warehouse.
This may include fulfilment performance in fulfilling orders (total mis-picks, mis-packs, etc.), total orders fulfilled by the hour to measure efficiency of staff, orders shipped on time, and much more.
A WMS can also help you with people operations by determining how many orders you plan to fulfil month over month and staff accordingly.
Having visibility into the day-to-day operations and access to inventory insights can help you make informed decision on how to better manage and optimise your warehouse.
4 warehouse inventory management best practices
Once you implement basic warehouse inventory management processes, you can then find ways to continuously improve your operations. Here are four best practices that can help create a more efficient warehouse:
1. Turn your employees into experts
By implementing ways to automate and streamline warehouse tasks, your team can spend more time finding ways to improve processes.
Your warehouse is only as efficient as the people who manage and work inside it. Be sure to leverage your team and ask for feedback on how to improve consistency, efficiency, and accuracy. The best ideas often come from those who are on the front lines.
If you lack a logistics team to begin with, many ecommerce businesses partner with 3PL that offer expertise in ecommerce warehousing, which relieves a lot of headaches for their logistics team.
2. Use demand forecasting for busy seasons
If your sales fluctuate seasonally or month-to-month, storage costs may become costly during the low season. A great way to optimise costs despite seasonality is by using demand forecasting tools to get answers to:
- How quickly products are selling
- Which items are slow-moving
- How many days of inventory you have until you are expected to run out (based on SKU velocity)
- How your sales are affected by different seasons and months
- What your best-selling items are and how they are performing compared to other periods
This type of data can help you better predict seasonality, so you can stock on inventory accordingly.
3. Automate warehouse inventory systems
By automating inventory and warehousing tasks and processes, you can quickly reduce the amount of time spent on managing inventory and picking and packing orders.
Many logistics automation solutions offer features that allow you to process orders automatically, create and manage inventory in real time, automatically update stock levels, offer the ability to set automatic reorder points, and much more.
This means your staff can avoid wasting time on mundane manual tasks and focus their efforts on speeding up the fulfilment process.
Need a WMS?
ShipBob has a best-in-class warehouse management system (WMS) for brands that have their own warehouse and need help managing inventory in real time, reducing picking, packing, and shipping errors, and scaling with ease.
With ShipBob’s WMS, brands can even leverage ShipBob’s fulfilment services in any of ShipBob’s fulfilment centres across the US, Canada, Europe, and Australia to improve cross-border shipping, reduce costs, and speed up deliveries.
4. Implement warehouse inventory control checks
As you grow your business, you will start to deal with more SKUs going in and out of warehouses. To make sure these stock items are not expired, old, or damaged, it’s important to conduct regular inventory control checks.
Order quality control helps you stay on top of suppliers, monitor each batch of inventory, and ultimately keep your customers happy by consistently delivering a quality product.
How ShipBob helps ecommerce stores with warehouse inventory management system
As your business grows, logistics become more complex. ShipBob is a 3PL that offers best-in-class fulfilment and logistics services, including a growing global fulfilment network, proprietary technology with built-in inventory management tools, and deep logistics expertise and support.
With ShipBob, you can store inventory in one or more of our fulfilment centre locations and have full visibility into the inventory and order management process all from one single dashboard.
Here is an overview of how ShipBob can help you optimise warehouse inventory management:
1. Warehouse management system
ShipBob’s fulfilment distribution network is powered by our proprietary WMS, which provides our merchants with visibility into the entire retail fulfilment process.
Unlike on-demand warehousing platforms, we own our entire tech stack, which empowers you with insights into exactly what’s going on in our warehouses, where your products are stored, and how many units you have on hand at all times.
From the ShipBob dashboard, you can search orders by tracking number, destination country, the number of items it contains, as well as get full transparency into performance such as fulfilment speed, orders fulfilled on time, error rates, and much more.
“Our old 3PL was unable to properly communicate amongst itself, both in regards to technology and people. We had to rely on a game of telephone and someone else to do everything for us.
Because of a lack of ownership of the entire fulfilment stack, it’s difficult to rectify, unlike with ShipBob who owns the entire stack: inventory and order management system, warehouse management system, and their ecommerce warehouses.”
Gerard Ecker, Founder & CEO of Ocean & Co.
2. Consistent warehouse optimisation
With ShipBob, ecommerce business owners can spend less time and money on inbound and outbound logistics, knowing that warehousing and fulfilment is being taken care of.
We provide the warehouse infrastructure needed, including worldwide locations, technology, and expertise. Once we receive your inventory, we follow standard processes to optimise storage to help save you on costs.
As your business grows, we can work with you to determine which other ShipBob locations it make sense to expand into.
By storing inventory in one or more locations, you better meet customer expectations around fast and affordable shipping by reducing the amount of shipping zones a package must travel through.
“As our business grew, fulfilling orders quickly became very time-consuming, and warehouse operations became a challenge. We found ShipBob, who checked all our boxes for a 3PL. They have ended up being the perfect solution for us and we have never looked back!”
Waveform Lighting Team
ShipBob is also constantly implementing new technology and automation tools to streamline the fulfilment process, such as automated sorting and box selection algorithms that uses dimensions and weights and your packaging preferences to tell us which package size to use for any order combination to provide consistent, predictable fulfilment pricing and a good customer experience.
3. Reporting and insights
ShipBob’s analytics and reporting tool can help you make better supply chain management decisions.
By connecting our merchant dashboard to our WMS, we’re able to provide you with insights into fulfilment performance, how we’re hitting our SLAs, visibility into order status and inventory counts, and much more.
You also get access to inventory and order data in real time. You can manage inventory movement, including when inventory is being received, stowed or put away, picked, packed, and shipped with the courier, which gives you full visibility into the entire process.
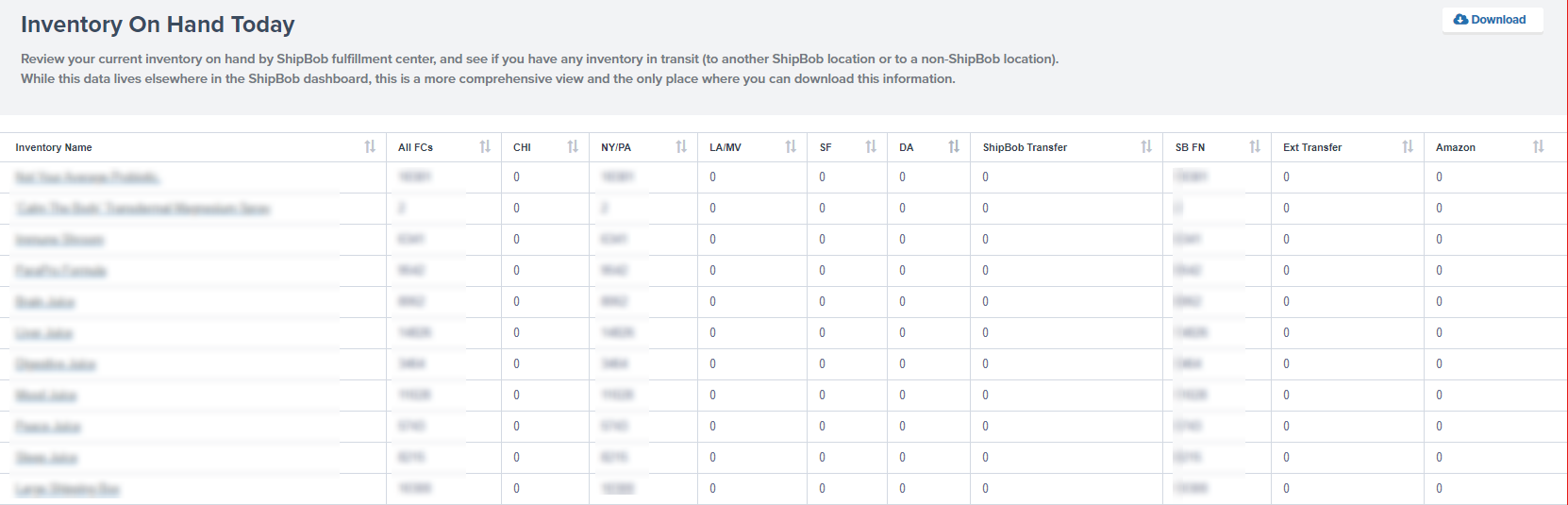
“ShipBob’s analytics tool is a game-changer and it’s helped me grow my business tremendously. It’s so easy for any of my team members to pull data in real-time. I felt like I couldn’t grow until I moved to ShipBob.
My CPA even said to me, ‘Thank God you switched to ShipBob.’ ShipBob provides me clarity and insight to help me make business decisions when I need it, along with responsive customer support.”
Courtney Lee, founder of Prymal
ShipBob is a tech-enabled 3PL with an international fulfilment network. We can help you grow your business by taking warehousing and time-consuming inventory tasks off your hands.
Warehouse inventory management FAQs
Warehouse inventory management is an essential component of the supply chain. Here are answers to the most commonly asked questions on the topic.
Warehouse inventory management FAQs
Warehouse inventory management is an essential component of the supply chain. Here are answers to the most commonly asked questions on the topic.
What is warehouse inventory management?
Warehouse inventory management involves receiving, storing, and tracking inventory in a warehouse, in addition to managing warehouse staff, to optimise inventory, logistics costs, and the fulfilment and shipping process.
How do you organise inventory in a warehouse?
One of the most common ways to organise inventory in a warehouse is to implement a warehouse slotting process, which streamlines picking and packing by storing inventory in a way that maximises efficiency for the picker. This process speeds up the warehouse picking and packing with less errors, optimises storage capacity, and reduces carrying costs.
Why is warehousing and inventory management important?
Warehousing and inventory management impacts your entire ecommerce supply chain, from receiving and storing inventory to fulfilling and shipping orders. Poor warehouse inventory management can lead to higher logistics costs, unhappy warehouse staff, more picking and packing errors, slower shipping times, and unsatisfied customers.